Tube Amplifiers Explained, Part 12: Power Supply, Rectification and Filtering
- Perry
- Apr 18, 2020
- 10 min read
Part of a blog series Tube Amplifier Circuits Explained
We have covered all the main parts of the amplification circuit. Now let’s back up and understand the power supply. Why are we doing this last? As you saw with the load lines and tube explanations, we have choices that we can make about the supply voltage and operating point that determine the voltage and current demands of the amplifier. Having this information helps understand the choices in the design of the power supply.
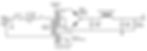
Looking at the schematic, let’s start on the primary side of the power transformer. Mains voltage comes in from your electrical outlet and we have a few components the hot side passes through in series.
First, a 2 amp fuse is for protection in case something in the amplifier is drawing more current than it should, such as if you had a short somewhere. We would rather the fuse blow than your components to be destroyed or amplifier to catch on fire, but even this fuse is not a guarantee that improper wiring or a short wouldn’t do damage to components, it just will break the circuit to prevent continuous high current that could be dangerous or cause a fire. This is a slow-blow type fuse, so it will allow a brief heavy draw of current, which is typical from the inrush that can happen when the amplifier is first turned on and capacitors are charged up.
Next, we have a negative temperature coefficient (NTC) thermistor. This is another protection device that has some amount of resistance when cold, and as it heats up over a few seconds, the resistance drops down closer to zero. This is to help reduce some of the inrush current of the amplifier when first turned on as the core of the transformer and capacitors are charged. It’s optional and the circuit would work without it, but there is a chance that the initial current is high enough to put a strain on some of the components. (In some circuits with large transformers, the inrush can even cause a circuit breaker in your house to be thrown.)
Finally, we have a simple switch to turn on or off the amplifier. When on, the hot side of the mains voltage connects to one lead of the primary side of the power transformer and the other lead of the primary closes the loop back to the neutral side of the mains.
Remember that a transformer uses two windings at a certain ratio to transfer power from the primary winding to the secondary winding and convert the voltage and current to different levels. In our case, we are using a transformer that will take 120V AC (U.S. mains voltage) on the primary, and we will get 650V AC on the secondary. This transformer is commonly used in tube amplifiers and it has two additional windings on the secondary side. One will provide 6.3V as the power for the tube filaments (heaters) of driver or power tubes. The other is 5V, which is commonly used for rectifier tube filaments. In our case, we are not using a tube rectifier, so this winding is not used or shown in the schematic. It is also common to not show the heater wiring in the schematic because it is relatively straightforward and is otherwise isolated from the rest of the amplification circuit.
You will notice that on this transformer the high voltage secondary has a center tap to use as a 0V potential. This is convenient so we can reference each 325V end of the secondary relative to this point; in some cases, the transformer will not have a center tap and you would use a slightly different type of rectifier to create a 0V reference. This becomes our ground reference throughout the amplifier circuit.
The transformer secondary is still AC, now at a higher voltage, but our amplifier will require a high voltage DC supply. In fact, we need this DC voltage to be as pure and steady as possible. The fundamental activity of the amplifier is to modulate this DC supply voltage based on the input signal. If the supply is not stable, we will not get a high-fidelity output and may even hear an audible hum or buzz. You’ll see why soon.
To convert AC to DC, we need a rectifier—something that will allow current to flow only in one direction, so we have only positive current. Amplifiers historically used a tube rectifier. From our earlier topic, you understand how a vacuum tube works—with a cathode emitting electrons and an anode pulling them in, allowing current. Importantly, this current can pass only in one direction. So using a rectifier “diode” tube (no control grid), you can rectify from AC to DC. Rectifier tubes drop a significant amount of voltage, require current to heat the filament, and add cost and physical space required in the amplifier. We have a better and cheaper solution now: silicon rectifier diodes. Once again, there may be debates about whether a tube rectifier is better: does it have a desirable “sag” under current loads impacting the sound and do guitar players prefer it in their amps, is it better to bring up the DC voltage slowly due to the heater warm-up time, what about switching noise of a diode, etc. I won’t try to cover the differences, but I will say that I believe diode rectifiers are very good at doing their job and are ideal for this amplifier kit, intended to be simple, high quality, and reasonable in cost. Using silicon diodes to rectify the power supply is very common in tube amplifiers and does not compromise the sound or make this a solid-state or hybrid amplifier in any way.
The AC voltage is cycling at 60Hz (US mains frequency) and each terminal of the high voltage secondary of the transformer is alternating back and forth at this rate, opposite from one another and positive or negative with respect to the 0V center tap. Diodes allow current to flow in one direction only and switch off when current goes the reverse direction. By connecting diodes on each secondary terminal, we create a two-phase rectifier. On the first half of the cycle when voltage swings positive on one terminal (with respect to center tap), that diode switches on and conducts current while the other terminal is now negative and that diode switches off. On the second half of the cycle, the opposite occurs and the other diode will conduct.

If you visualize the effect of this at the output of the rectifier, the voltage potential with respect to the center tap is always positive—first from current flowing through one diode for the first half-cycle, and then from current flowing through the other diode for the second half-cycle. The rectified voltage now looks like the graph below.
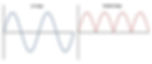
We are making progress, but our intention is to have smooth DC voltage, not large peaks and voids like this. We need to filter this power supply to smooth this out. There are various ways to do this, but the two main components to use are capacitors and chokes (inductors).
By putting a capacitor in parallel with our supply voltage, the rectified voltage will charge it up on the up-cycles and then when the cycle is falling, the capacitor will discharge, supplying current to the amplifier load. You could call this a “reservoir” capacitor because it’s like we have a tank holding a supply of water. While the faucet may be turned on and off continuously to keep it filled, we can tap the barrel from the other side to draw a relatively steady stream out.
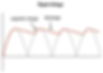
A reservoir capacitor will make our DC voltage look like the chart here. Note that we still have some ripple voltage as the capacitor is discharged, but it’s certainly better than the peaks we had previously. In our circuit we are using a 220uF capacitor as our reservoir capacitor. You could use a lower or higher capacitance. I will not try to describe the calculations of what size ripple voltage you would have for a given power supply, capacitor, and load, but the point right now is that we have more work to do, even after putting in place this capacitor.
If we used this DC as our B+ supply, this ripple voltage would be modulating our plate voltages by a small amount at a frequency of 120Hz (since this rectified voltage represents two half-cycles of the original 60Hz AC). You would hear this as a sort of buzz or hum in your amplified output.
We can do more to continue to refine this power supply and get the DC supply as clean as possible, with ripple below any audible level. While you might just be tempted to use a bigger reservoir capacitor, there are limits to how much this can reduce ripple, and has some other downsides I won’t go into here.

What we are attempting is to allow DC to pass while we filter out the frequency of this ripple—think of it like AC at 120Hz riding on top of the DC current. One technique would be a low-pass RC filter—using a resistor and another capacitor to create a type of voltage divider that would attenuate frequencies above a certain point. This type of filter is inexpensive and could work, but the resistor will require some voltage to drop, sort of wasting a bit of our power supply, dissipated as heat and resulting in a B+ voltage not as high as we could otherwise have. Sometimes this is the right answer, but another option is to use an inductor, in this case called a choke. We can put it with another capacitor to have an LC filter (inductors typically denoted with the symbol L).
Remember we covered that capacitors block DC but allow AC (a simplistic way of describing it). And inductors are the opposite, reacting against AC current changes while allowing DC to pass. Putting the inductor in series in our filter will have minimal impact on DC, while reacting against the AC change at the ripple frequency. There are some downsides to using a choke. Most notably they can be expensive and heavy when they have enough inductance to do adequate filtering. In our case we are using a 6H choke (inductance measured in Henries) and it has about 150 ohms of DC resistance, since all wires have some amount of resistance. DC resistance in a choke is generally not the intention and becomes another factor in selection/cost, though at times you may want a bit more DC resistance. We are then using another capacitor, this time a lower value of 56uF as the last part of the filter.
So looking again at our schematic, we have our rectified power supply going through a capacitor-inductor-capacitor sequence. The end result is a filtered B+ that should have very little ripple voltage, which means our amplifier should have a clean power supply we can use for an amplified audio signal, and silence when there is no signal.
How much DC voltage will we get as our B+ after this rectification and filtering? First, remember that AC can be measured in RMS volts, sort of like an “equivalent” steady voltage measurement because it’s actually changing voltage throughout its cycle. This transformer is designed to provide 650V center-tapped (usually labeled 325-0-325), meaning 325V RMS on each half-cycle of the secondary that we have rectified to be a positive voltage, which means the peaks you see in the illustration are going a lot higher. A commonly used formula is that peak voltage is the RMS voltage times 1.41, so our 325V RMS is actually a voltage that could reach almost 460V at the peaks, and this is what our reservoir capacitor is being charged up with. Each diode will typically drop a small amount of voltage, and the choke has some DC resistance in its winding, too. So our final B+ supply turns out to be around 420V. (We had estimated in earlier topics a supply voltage of about 400V DC, so this is pretty close, and actually the circuit was optimized for a bit higher B+ but I used 400 to make the explanation and charts easier.)
A few notes on component ratings. First, the diodes used in the kit are rated for reverse voltage up to 1200V. I sometimes use common types of diodes rated for 1000V, but this is a bit of a risk if our peak voltage is around 460V, meaning the peak to peak voltage from the 460V charging the capacitor to negative 460 on the reverse cycle of the diode would total 920V, and there can easily be some plus/minus variation in mains voltage or in the transformer. So to be safe, we are using higher rated diodes.
The capacitors are rated to 500V. Even though our final B+ may come out below 450V and it’s easier and cheaper to find capacitors rated at 450V, the voltage at startup with no load and as the capacitors first charge can easily exceed 450V. Most capacitors can handle a bit of excess, but it’s not worth the risk and potential shortening of lifespan.
We should also talk about current demand of the circuit. Transformers are rated for a certain amount of current. The one used in this kit is rated for 207mA. If we add up the demand of our expected circuit based on our load lines, we would have approximately 65 mA per channel for the power tubes and 5 mA each for the driver stage, totaling around 140mA or so.
There is also a current demand of the heaters. Each EL34 requires about 1.5A and the 12AT7 requires 300mA, for a total of 3.3A. This is rated separately on the transformer, and ours can supply up to 4.5A of heater current at 6.3V.
There is one final component on the power supply we haven’t touched on, the 330k bleeder resistor. This is for safety reasons. When you shut off the amplifier, this will take a few seconds to dissipate the energy that has been stored in the capacitors so they are at a safe level. If somehow you had no load on the circuit but charged up the capacitors, you could turn off the amplifier and unplug it and there could still be a very dangerous high voltage charge in the capacitors hours or even days later. A very small amount of wasted current through this bleeder is worth the safety of not having a surprise shock.
There is far more depth to power supply design than I’m able to cover, and other very different techniques that could be used to regulate voltage or current. In this kit, you are seeing one design and hopefully this helped explain the basic principles of transforming the AC voltage, regulating it to DC, and filtering it.
One last post coming next to bring the entire circuit together!